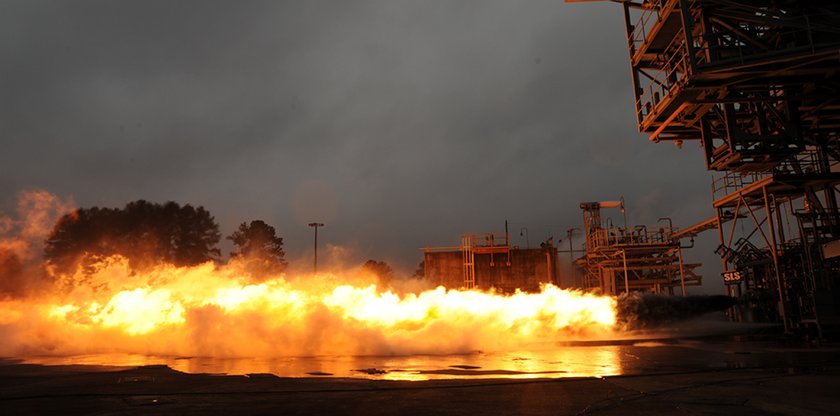
HUNTSVILLE, Alabama – Engineers and scientists in the Huntsville area are using next-generation manufacturing techniques and the latest advances in rocket engine technology to build cost-efficient hardware aimed at lifting U.S. ambitions in space and safeguarding security at home.
Dynetics, a Huntsville firm with roots dating back 40 years, and partner Aerojet Rocketdyne are leaders in the effort. The team is utilizing 3-D printing and other sophisticated manufacturing methods to produce an updated version of the Space Race’s crown jewel – the powerful F1 rocket engine used in the Apollo program.
NASA awarded Dynetics a contract in 2012 to study whether it was possible to develop an affordable American-made booster engine based on the Saturn V’s proven F1. Since then, NASA has added other work to the contract for the Dynetics team to design, fabricate and test key components of another rocket engine under development, called the AR1.
“Alabama is leading in developing advanced manufacturing techniques in low-cost, affordable, complex space systems, both in rocket engines and the launch vehicles themselves,” said Steve Cook, vice president of corporate development for Dynetics. “That technology is here, and we will continue to utilize it and put it into future programs.”
The AR1 is being advanced for use in NASA’s Space Launch System (SLS), a project being led from Huntsville’s Marshall Space Flight Center to make a return trip to the moon and eventually take man to Mars. Initial SLS flights will be powered in part by solid rocket boosters similar to those flown for the Space Shuttle program, but later missions will require more powerful boosters.
“Whether we want to go to the moon, an asteroid or Mars, we’ve got to have a heavy lifter,” Cook said.
In addition, the AR1 is seen as an American-made replacement for the Russian RD-180 engines used on the United Launch Alliance’s Decatur-made Atlas V rockets, which blast critical national security satellites into orbit. Amid diplomatic tensions with Russia, Congress has decreed that the RD-180 must be replaced with a U.S-made engine on those launches by 2019.
FROM MONTHS TO DAYS
Cook said the Huntsville team’s goal is to build low-cost liquid-fuel rocket engines and produce them quickly in a way “that completely breaks the cost paradigm.”
“We had a design that we know works, but it would be too expensive to recreate,” he said. “In the Saturn-Apollo era, they threw money at the problem, and they were literally creating the art at the time. They created this masterpiece called the F1 engine. It worked well, successful on every mission.
“So we said, ‘Let’s take this engine design we know works but make it modern. Let’s get the cost down and bring the reliability up,’ ” he added.
New technologies and advanced manufacturing techniques are making that possible. The Huntsville team used additive manufacturing – also called 3-D printing – to build a critical engine component, the gas generator injector, in just 15 days, plus a few weeks of additional machining time. In the 1960s, the complex part took 15 months to manufacture. The new version is lighter and cost significantly less to make.
“We’re getting ready to put that part in the test stand this summer,” Cook said.
If the team gets the go-ahead to build the AR1 rocket engine, the main propulsion system final assembly is planned to take place in Decatur, according to Aerojet, which last year located its Advanced Hydrocarbon Propulsion Development Office in Huntsville.
“It’s our intention to do the long-term manufacturing here in Alabama,” Cook said.
As part of its work on SLS, Dynetics figured out a novel way to fabricate a cryogenic tank that’s needed to hold the rocket engine’s liquid fuel at temperatures up to minus 350 degrees. The traditional method of making the tank barrel involved a considerable amount of machining on individual aluminum sheets that were rolled into a curve and welded together – a labor-intensive process.
“We came up with an approach that removes 75 percent of those welds, and we’re testing the tank right now,” Cook said. “It was built right here in Alabama.”
To make the tank, Dynetics devised a method to essentially take a single 10-foot by 58-foot sheet of aluminum, roll it into a circular shape 18 feet in diameter and seal it with a single weld using friction stir welding tools that had been installed at Marshall for NASA’s Ares rocket program. Cook knew the equipment was there because he had managed Ares before its cancellation.
Weighing in at more than 10,000 pounds, the cryogenic tank barrel is the largest tank built at Marshall since the Apollo era. It’s now at the Dynetics facility in Iuka, Mississippi, for testing to verify its structural design and manufacturing processes meet all of NASA’s requirements.
EVOLVING BEYOND DESIGN
Dynetics also has been tapped by Boeing Co. to produce some key elements to ensure the success of the SLS core stage. In Huntsville, Dynetics engineers are producing structural simulators, 27 feet in diameter, that will be used to test the structural integrity of the SLS core stage. The simulators are replicas of the core stage, which towers more than 200 feet and houses the vehicle’s avionics and flight computer. The core stage also stores cryogenic liquid hydrogen and liquid oxygen that will feed the engines.
In addition, Dynetics is designing, building and testing thrust vector control flight hardware for the SLS core stage.
“We’re building the hardware that helps steer and point the rocket, so not only is Dynetics and North Alabama key to the structural integrity of the rocket, we’re also key to keeping it pointed in the right direction,” Cook said.
Cook believes the Huntsville area and North Alabama are well positioned to evolve from a center of rocket design and development to a more vertically integrated hub where the manufacturing and testing of launch vehicles also takes place.
“The future definition of the ‘Rocket City’ is that we’re building more rockets, not just designing them in Huntsville. We’d like to be in the lead of that next wave of space vehicle manufacturing and design and development here in North Alabama,” he said of the Dynetics rocket breakthroughs.
“It’s a great evolution. I would argue that it is exactly what Wernher Von Braun intended when he came to Huntsville in the 1950s. We started out doing that in the 1960s and then we sort of pulled out in the 1970s; now, you’re seeing a renaissance. The cool thing is that it is cutting edge, using state-of-the-art technologies.”
Don’t miss out! Subscribe today to have Alabama’s leading headlines delivered to your inbox.